We’re here to help and want to address your frequently asked questions. Reach out if you still have questions.
For our premium users, we'll send you a setup package with all the required hardware, including a small form factor server, two hubs, power cables, and mounting accessories. Read this blog for a full breakdown of the implementation process.
The PICO server is an Intel NUC with a standard capacity of 500GB SSD which is more than enough storage to sustain a factory for a few years. A higher-power PICO server is available if needed.
Yes, we can help you run your instance of PICO on cloud-based servers.
PICO hardware comes pre-loaded with our proprietary software, and we manage your server for you, so you don't have to worry about running patches, software updates, or general maintenance. Installation is as simple as plugging in and connecting your tools. Learn more about our IT infrastructure.
PICO adheres to the regulations established by SOC 2 and ITAR compliance standards.
If your company uses Microsoft Authentication, we can deploy a MS OAuth application in PICO so that approved users can log in with their MS credentials.
Implementing PICO is easy to set up and only takes a few hours. The process is remote and doesn't require dedicated IT resources. You can start error-proofing your factory right away.
PICO integrates with a variety of commercially available shop floor tools. Check out our complete list of Connected Tools.
Yes, our Device Integrations team takes requests for new tools. We also update our library on a monthly basis. You can suggest a new tool here.
Our device integrations team does the heavy lifting for our customers so that tools are truly plug-and-play. Just select your tool from our library of over 200 connected devices, and you're ready to build. See what one customer has to say about the convenience of our connected tools library.
We created an intermediary device that enables these kinds of tools to work with PICO. Read about in this blog post.
There is no limit to the number of tools per workstation. Your tools connect to the PICO Hub, and you can assign as many Hubs as you need to get all your desired tools into a station.
We integrate with SAP, PLEX, NetSuite, Infor, and Odoo. We will continue to grow this list as customers request new integrations.
PICO has a user-friendly interface for creating your digital work instructions. Through pictures, videos, BOM tables, and other graphic design tools, your processes and products can quickly come to life as step-by-step instructions for your operators. Sign up for free to start creating digital work instructions in PICO!
Yes, in PICO we refer to this functionality as process variants. For high-mix assemblies, you can create a template process with unlimited variant processes that have unique deviations in one or more steps.
Process variants can be used to easily set up translated versions of your work instructions.
Yes, change control is a required step before any changes to work instructions are deployed to the workstations. Approval processes are not included in the Basic plan.
PICO captures progress through work instructions, direct outputs from connected tools, manual measurements, and any notes or alerts associated with each build. Every piece of data we collect is contextualized, so it can be easily traced to a particular part, work instruction, station, and operator. Learn more about automated data capture in PICO.
The data captured in PICO serves as a great resource for analytics on defect tracking, cycle times, throughput, and more. See how one customer finds value in digital data collection.
Your data is stored locally on your factory's PICO server. We offer encrypted backups to both AWS and GCP in the cloud that can also be configured to live on-premise if needed. See how we protect your manufacturing data in ITAR and other strict IT environments.
You can submit a request to our customer support team via email, Slack, or MS Teams and they can quickly build out custom cloud-based dashboards to meet your needs.
PICO offers a basic quality notes system that allows you to record and categorize quality issues. This data can be further analyzed via SQL and can be exported out to other systems such as an ERP.
Gain access to hundreds of solutions from a single platform
Step into the future of factory operations with Pico MES. Start your journey toward a more efficient, error-proof factory floor today.
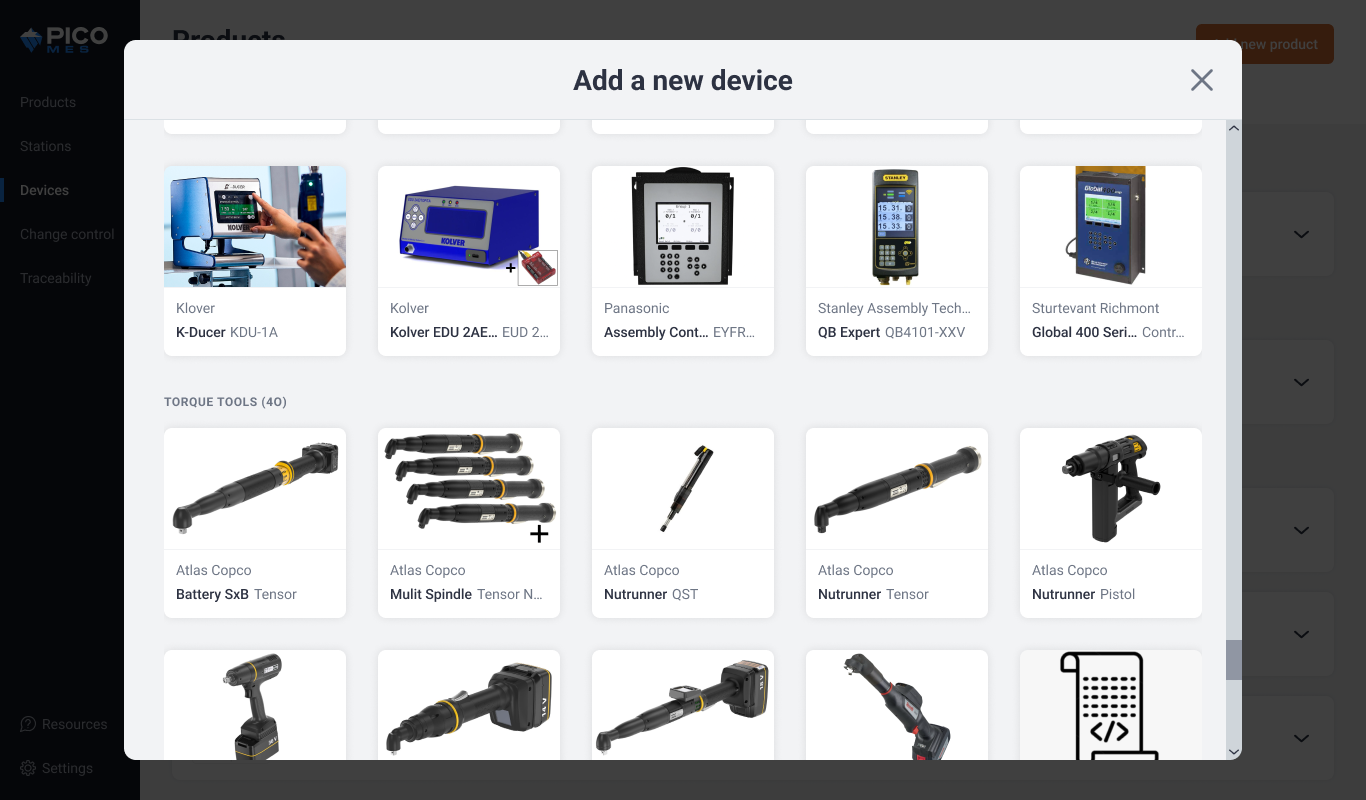